An innovative and unique fusion of FDM 3D printing with composites.
Our distinctive slicer software enables the design and printing of lightweight yet rigid parts, and our large-scale FDM printer machines make it cost-effective to produce them in large dimensions. By encapsulating lightweight, stiff materials within a layer of robust fiber reinforcement, we create a sandwich structured composite that is ideal for constructing applications where an emphasis is placed on both light weight and high strength/stiffness.
Industries such as aerospace, marine, and transportation are just a few examples that could reap the advantages of the minimal time lapse between digital design and the availability of a functional prototype, ready for real-world testing of both performance and ergonomic considerations. By bypassing the costly and time-consuming step of mold creation during the prototype phase, it becomes possible to iterate at a significantly faster pace, with each iteration cycle measured in days rather than weeks or months. Once content with the prototype's performance, the final 3D printed and laminated prototype can be meticulously finished to achieve an A-class surface quality. From this, a durable female mold can be crafted for use in production.
In contrast to CNC machining of foam cores, 3D printing offers numerous advantages. It is typically more cost-effective, generates minimal material waste, provides a wider range of base polymers to choose from, and allows for the production of complex geometries with significantly thinner sections.

Variable core thickness & density
With 3D printed composite cores, achieving continuous variations in core thickness and density becomes straightforward, allowing for optimized designs without the need for additional manufacturing steps or complexities. Furthermore, it's possible to directly incorporate high-density regions into core panels at load-bearing points, as well as integrate various attachments such as threaded inserts or studs into the design.

Composite core inner geometry
The cornerstone of this technology lies in our capability to rapidly and consistently 3D print lightweight patterns, which serve as the cores for the composite skins. Due to the direct generation of GCode from the model, bypassing the intermediate STL/slicing process, we have complete control over not only typical print parameters such as speed, nozzle temperature, and retractions but also the ordering and segmentation of print lines, line widths, layer heights, and more. When combined with highly efficient infill structures that closely follow outer contours, surpassing the fixed infill meshes commonly employed in standard slicers, we can achieve structural properties that rival or even surpass traditional foam and honeycomb cores. All the while, this approach remains cost-effective for serial production.
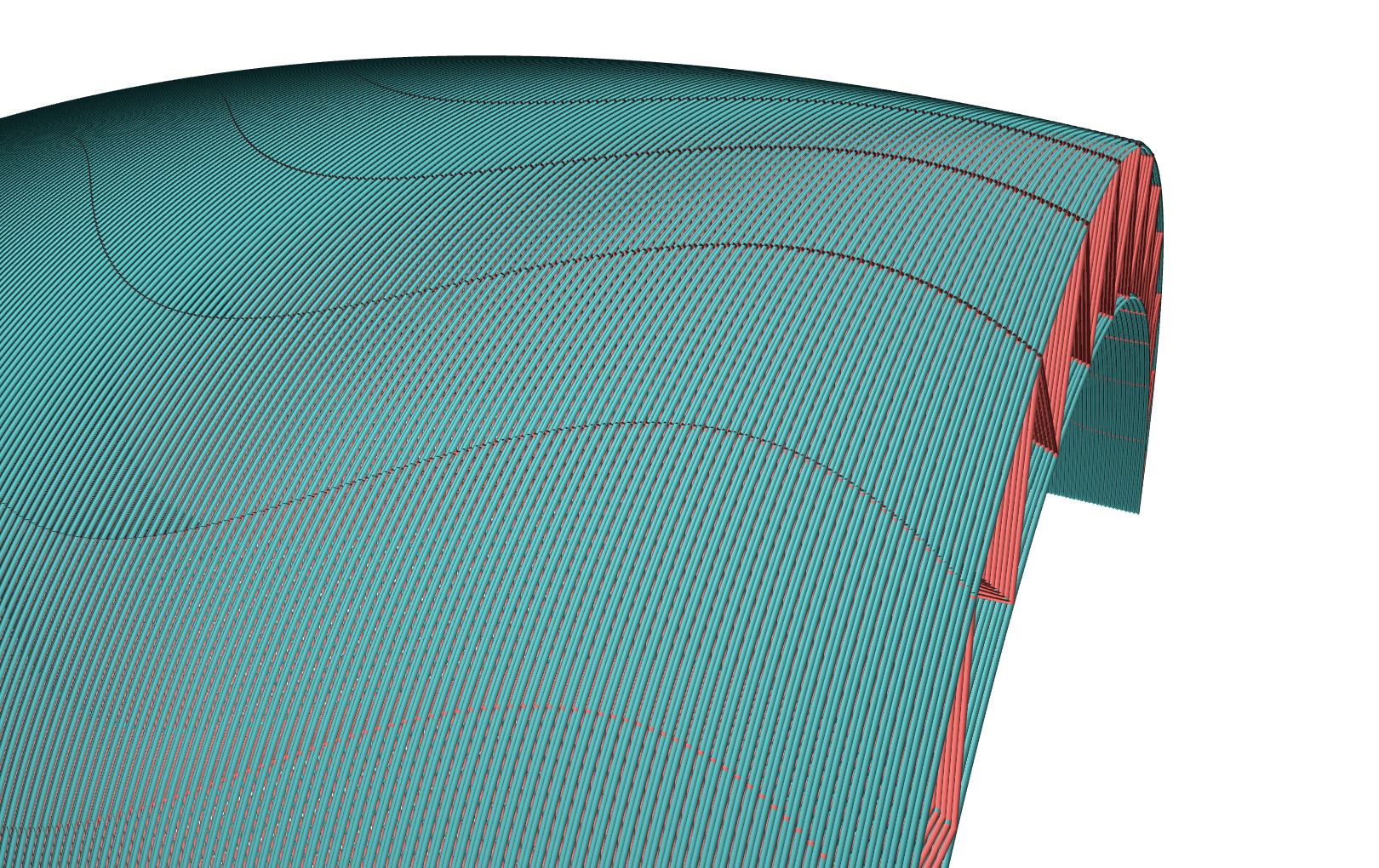
Surface texture
To ensure a strong bond between the epoxy composite skins and the 3D printed core, we have devised a unique ribbed surface texture. Furthermore, apart from enhancing the bond, this ribbed surface texture also enhances surface stiffness. Unlike a fuzzy-skin texture, it doesn't compromise print speed or exacerbate print-head vibrations.